Custom Collapsible Cage Pallet Solutions for Industrial Storage
2025-03-19 15:33
In high-demand industrial operations, efficient storage and material handling are mission-critical. A recent client faced a pressing challenge: designing robust, space-adaptive containers capable of supporting heavy loads while optimizing warehouse footprints. Mybox, a leader among cage pallet manufacturers, delivered a tailored collapsible cage pallet system that combined durability with logistical flexibility. This case study reveals how the solution achieved 30% faster warehouse turnover and 40% lower logistics costs.
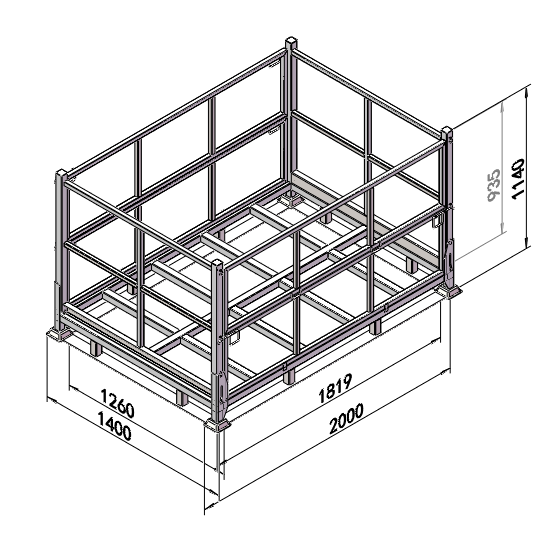
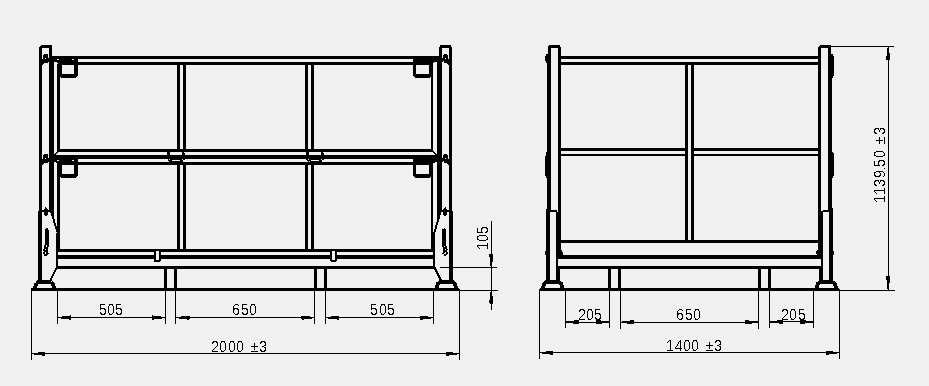
Challenge: Balancing Strength, Space, and Scalability
The client required containers to:
-
Withstand Heavy Loads: Static capacity of 400kg–2 tons for machinery parts and raw materials.
-
Maximize Vertical Space: Safe 3-layer stacking without compromising stability.
-
Adapt to Dynamic Workflows: Foldable design to reduce storage space by 70% when idle.
-
Optimize Dimensions: Sizes from 1200×1000×900mm to 2000×1400×1140mm for varied inventory.
Solution: Engineering Precision by Leading Cage Pallet Manufacturers
Mybox’s collapsible cage pallet system addressed these needs through:
1. Heavy-Duty Construction
-
Materials: Carbon steel frames with cold-galvanized coating for corrosion resistance in harsh environments.
-
Load Optimization: Reinforced base plates and laser-welded joints supported 2-ton static loads (2-layer safe stacking).
-
Foldable Mechanism: Patented hinges enabled vertical collapse to 240mm height, ideal for return logistics.
2. Customizable Configurations
-
Door Flexibility: Removable/foldable doors (2000mm side) and half/full-access panels (1400mm side).
-
Modular Add-Ons: Optional lifting hooks, lockable casters, and mesh/solid flooring for diverse workflows.
3. Space-Saving Logistics
-
Collapsible Cage Pallet Stillage Design: Interlocking base feet ensured 3-layer stacking stability.
-
Shipping Efficiency: 40HQ containers held 56–126 units (depending on configuration), reducing freight costs.
Results: Efficiency Gains and Cost Savings
The collapsible cage pallet stillage system delivered:
-
30% Faster Turnover: Quick-access designs and foldable storage streamlined inventory management.
-
40% Lower Logistics Costs: Reduced shipping volume and reusable packaging minimized expenses.
-
ISO 9001 Compliance: Rigorous load-bearing tests validated safety for global operations.
Technical Specifications
Feature |
Details |
Dimensions (L×W×H) |
1200×1000×900mm – 2000×1400×1140mm |
Load Capacity |
400kg (dynamic) / 2 tons (static) |
Folded Height |
240mm (max) |
Material |
Cold-galvanized carbon steel (Q235) |
Best Practices for Collapsible Cage Pallet Stillage
-
Safe Handling: Use forklifts at ≤5 mph to prevent frame stress.
-
Routine Inspections: Check hinges, welds, and base feet quarterly for wear.
-
Stacking Alignment: Ensure interlocking feet are fully engaged between layers.
Why This Matters for Industrial Storage
This project highlights how collaboration with innovative cage pallet manufacturers can transform logistics:
-
Modularity: Configurable designs adapt to evolving operational needs.
-
Durability: Cold-galvanized finishes extend lifespan in corrosive environments.
-
Sustainability: Reusable collapsible cage pallets reduce waste vs. disposable alternatives.